There are numerous processes by which jewelry is made. The work in my collection is crafted either through fabrication or the lost wax casting process. This article will outline some basic techniques used to work with non ferrous metals. Non ferrous metals include brass, silver, gold, platinum and those that do not contain iron and therefore resist rust. Although ferrous metals are also commonly fabricated many of the methods used to manipulate them will differ from those used with non ferrous materials. Unlike casting, fabrication starts with metal components that are joined through either cold connections like rivets, or heat with soldering or brazing.
Some projects require machining to create components. Others entail rolls of wire, sheet metal and an array of pliers of differing shapes and/ or hammers, which likewise could apply any assortment of textures. My favorite and by far the most interesting tool in my workshop is my BC Ames lathe. It is a turn of the century machine that was passed down to me from my grandfather. It was a tool critical to his livelihood and now it is one that I use regularly in mine.
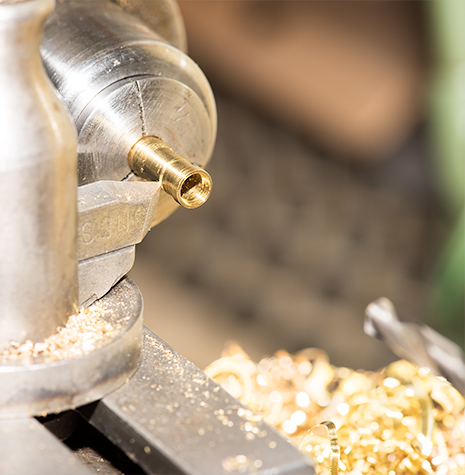
Through fabrication every item is made from start to finish every time. For the most part there are no molds made to eliminate steps. However, while producing these projects I often streamline the process by organizing my work in an assembly line fashion on my bench. Cast items can require one hundred hours or more on an original model to be molded, fabrication is normally a far shorter process with few exceptions. While components of sheet metal and wire are individually crafted each time, I do occasionally create models for cast findings to use as stone settings for some of my designs. This combines the two processes of casting and fabrication.
Machining a finding to be used as a model for a stone setting can be a tricky endeavor. These projects must be accurate to around 100th of a millimeter, and shrinkage must also be carefully accounted for. I am not too proud to mention that creating models for stone settings is something that normally takes me some trial and error. This level of accuracy requires intense focus and precision. Also consider that some aspects of a finding can be easily measured with verniers while others take a degree of guesswork. Silver does not machine well so using cast components like bezels is far more efficient in both workability and waste. The value of the silver that would be temporarily lost by turning down thick silver stock would be massive if each bezel were individually turned.
After each component of a design has been formed I align everything up on a soldering pad. An army of pendants or earrings is tackled in batches. Parts are formed, soldered, polished and if there are stones they are all set either before or after polishing depending on the setting style. I favor prong and bezel settings but occasionally flush set or otherwise mix things up.
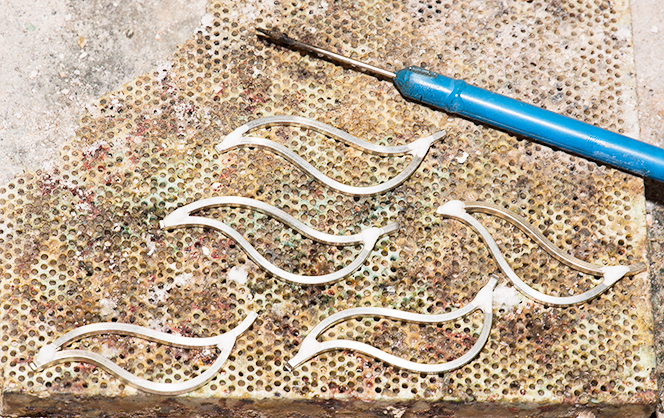
Every step in the fabrication process is deeply involved. These processes among others that I did not delve into could be explained in far greater detail. Blogs exploring some of the interesting facets of fabrication will follow as the inspiration to write them strikes.