Virtually any jewelry supply catalog has a variety of wax carving tools to choose from. However the vast majority of them are exceedingly large. These are wonderful for roughing out a design quickly. Although, they make it virtually impossible to achieve fine detail or navigate the awkward angles sometimes required by a complex piece. Only in recent years have I seen some more petite carving tools reach the market. These instruments look fantastic and I know I would truly enjoy carving with them if it weren’t for the cost. Somehow these tiny gadgets pack a hefty price tag. Not withstanding the fact that my tool collection has been developing for many years. At this point in my career, it is rare that I encounter a shape that I do not have the ideal implement to accommodate, though occasionally it still happens.
Some of my favorite tools include, yes, a couple of the store bought commercial variety, and many that I have made or shaped myself. One of the first that I developed a great affinity for was actually designed for ceramics. It had a curved edge on one end and knife edge on the other. In my younger years I dabbled in sculpting clay and held on to many of the necessary accessories to this craft. This one in particular does not hold an edge quite as well as it could, but that quality is not entirely negative, as I will explain later. I used this tool in my debut line of Zodiac Ponies, the collection that I began my business with. I still use it for projects today though less often.
Dental tools are wonderful to reshape! Many of them are already bent to various angles that prove quite beneficial. My filigree projects have required quite an assortment of custom tools. The nature of these hollow seamless shapes automatically entails unusual angles and fine detail, involving undercuts and greater levels of three-dimensionality further demand special consideration.
When dental picks are not within reach, thick stainless steel wire can be mounted in the end of a small dowel and ground into virtually any shaped blade with brilliant results. Bike spokes are particularly desirable in this regard. Stainless steel will hold an edge beautifully and require only intermittent sharpening.
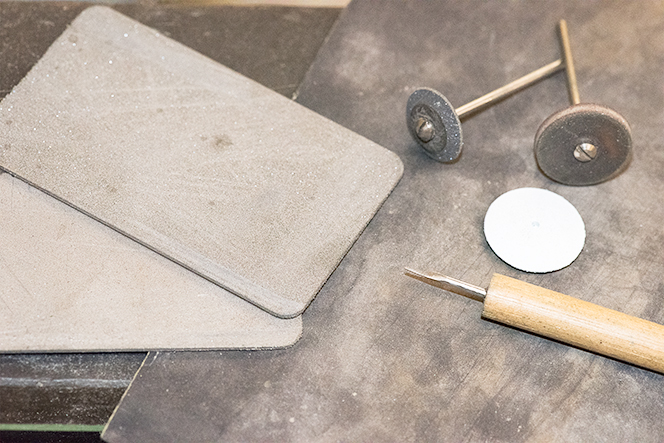
Heatless mizzy wheels, sanding disks, or virtually any rubber wheel can be used to shape and sharpen. It is necessary to keep some water on hand to dip the tool sporadically. If steel is heated to the point where it changes color, it becomes annealed or softened. Annealed steel will not hold an edge. Sanding stones and sand paper laid atop glass works beautifully to refine the edge. Any striation or imperfection in your blade will invariably be applied with every stoke to your design. Admittedly, my patience is always tried when it comes to administering a perfect finish to a tool.
The question of how sharp your blade should actually be is another topic to consider. To one with no wax carving experience it might seem immediately obvious that only the very sharpest should be used. Though anyone with some experience can tell you that those are, in fact, the most challenging to carve with. In my early years I actually dulled the edges of some of my commercial tools (which I later corrected). The reason being, sharp tools can catch and skip while a softer edge will naturally burnish.
While in school, I actually heard two different professors contradict each other completely on the topic. One claimed that only sharp blades should be used while the other stood by his opinion that they should never be used.
My conclusion is based more on circumstance than one fixed method. Initially as a beginner it is easier to learn by carving with a softer edge. Beginner work is typically less intricate and does not require the delicate touch that a sharp blade can provide. As designs become more elaborate and detail finer, a dull edge will force too much pressure upon the design and the wax will break. Much of my current work is exceedingly delicate while in wax. Filigree and light open work requires extremely sharp instruments and a feather light touch. The length of time demanded by a carving increases dramatically with fine delicate details because only small shavings of wax can be scraped off and only very gradually.
Dental picks and the likes work wonderfully for wax carving, although many other applications could also reap their benefits. Undoubtedly projects involving clay, plaster, pmc, or virtually any other sculptable material could be improved in quality and efficiency with a greater variety of tools.
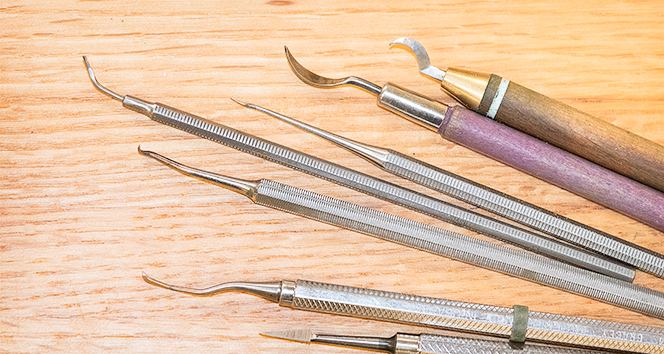